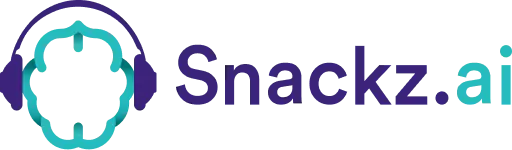
Enjoying Snackz.ai?
Sign up!
or
I agree to the Privacy Policy and the Terms of Service.
Already have an account?
๐ฉ Check your inbox!
A link to reset your password has been sent to your email address.
Reset Password
No worries! Just enter your email below, and we'll help you reset that password:
Enjoying Snackz.ai?
Sign up!
or
I agree to the Privacy Policy and the Terms of Service.
Already have an account?
๐ฉ Check your inbox!
A link to reset your password has been sent to your email address.
Reset Password
No worries! Just enter your email below, and we'll help you reset that password:
โก Free 3min Summary
"The Toyota Way" - Summary
"The Toyota Way" by Jeffrey K. Liker is an insightful exploration into the management principles and business philosophy that have propelled Toyota to the forefront of the automotive industry. This book delves into the 14 key principles that form the backbone of Toyota's success, offering practical advice for businesses aiming to enhance their processes, eliminate waste, and foster a culture of continuous improvement. Liker's expertise and detailed analysis make this book a must-read for anyone looking to understand the secrets behind Toyota's efficiency and reliability. By adopting these principles, businesses can achieve remarkable improvements in quality, productivity, and employee engagement.
Key Ideas
The Elimination of Waste (Muda)
Central to "The Toyota Way" is the relentless pursuit of eliminating all forms of waste in every process. This includes overproduction, waiting, unnecessary transportation, overprocessing, excess inventory, defects, and unused employee creativity. By meticulously identifying and removing these inefficiencies, Toyota optimizes its operations for maximum value creation, ensuring that resources are used effectively and costs are minimized.
Continuous Improvement (Kaizen)
Toyota fosters a culture of continuous improvement, where every employee is empowered to identify problems, suggest solutions, and implement changes. This bottom-up approach ensures that improvements are driven by those closest to the work, fostering a sense of ownership and engagement throughout the organization. Kaizen encourages small, incremental changes that accumulate over time, leading to significant long-term gains and a dynamic, adaptive business environment.
Respect for People
Beyond its focus on efficiency, "The Toyota Way" emphasizes respect for individuals and teamwork. The company invests heavily in its employees, providing extensive training and development opportunities. By creating a collaborative and supportive work environment, Toyota encourages employees to reach their full potential and contribute to the company's success. This people-centric approach fosters loyalty, motivation, and a shared commitment to excellence, making it a cornerstone of Toyota's enduring success.
FAQ's
"The Toyota Way" discusses 14 key principles that are essential to Toyota's success. These principles include the elimination of waste (Muda), continuous improvement (Kaizen), and respect for people. Each principle is designed to enhance efficiency, productivity, and employee engagement within the organization.
"The Toyota Way" approaches continuous improvement through the concept of Kaizen, which empowers every employee to identify problems, suggest solutions, and implement changes. This bottom-up approach ensures that improvements are driven by those closest to the work, fostering a sense of ownership and engagement throughout the organization.
Respect for people is a fundamental principle in "The Toyota Way" because it emphasizes the importance of investing in employees and creating a collaborative work environment. By providing extensive training and development opportunities, Toyota encourages employees to reach their full potential and contribute to the company's success, fostering loyalty, motivation, and a shared commitment to excellence.
๐ก Full 15min Summary
Let's dive into the history and evolution of the Toyota Production System, in short 'TPS', and the Toyota Way. Our journey begins with Sakichi Toyoda, the founder of Toyota. Sakichi was an inventor who created automatic looms. His approach to constant improvement through trial-and-error experimentation became a cornerstone of Toyota's philosophy.
The baton was then passed to Sakichi's son, Kiichiro, who established the Toyota Motor Company. Kiichiro's time in England studying waste in loom production sparked the development of key TPS concepts such as just-in-time and built-in quality. Post World War II, Toyota leaders, including Eiji Toyoda, were tasked with the challenge of matching US productivity. To tackle this, Taiichi Ohno spearheaded the development of TPS.
Ohno expanded on Kiichiro's ideas, enhancing the just-in-time concept with the introduction of kanban pull systems. His primary focus was on eliminating seven forms of waste to create a smooth workflow. Overproduction was seen as the most detrimental waste as it led to excess inventory and concealed underlying issues. Ohno crafted unique solutions tailored to Toyota's specific needs in a small-volume, high-variety environment.
One key aspect that stands out in this journey is the continuity of leadership and philosophy across generations of the Toyoda family. They championed hands-on problem-solving and a sense of responsibility towards society. TPS evolved through scientific thinking to address Toyota's unique challenges, eventually becoming a new paradigm in manufacturing.
However, the technical tools of TPS are not the secret to Toyota's success. The real magic lies in the underlying philosophy and culture that drive the system. Attempts at lean implementations that only scratch the surface often fall short because they fail to cultivate the necessary culture, engage all employees, and adopt a holistic systems approach. The principles of TPS embody the spirit of the Toyota Way, which is all about accepting challenges and responsibility with a positive outlook and a sense of self-reliance.
Enjoyed the sneak peak? Get the full summary!
Explore Books
Let's find the best book for you!
Get book summaries directly into your inbox!
Join more than 10,000 readers in our newsletter
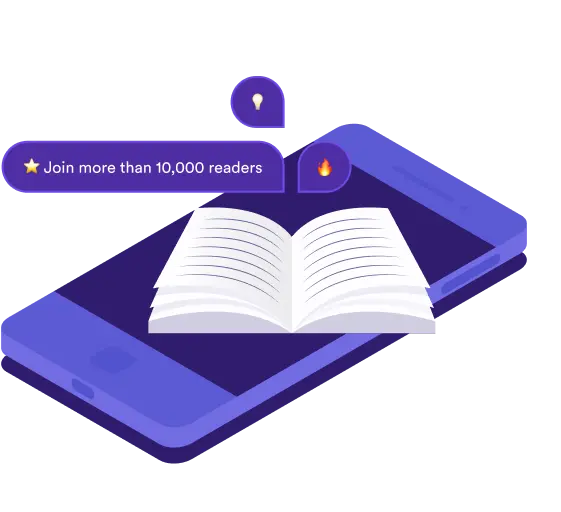
Discover the Snackz AI catalogue
Get the books directly into your inbox!
โ New Release
โ Book Recommendation
โ Book Summaries
Copyright 2023-2025. All rights reserved.